Manufacturing
Capturing data from the shop floor is a big challenge in the manufacturing operations. With ERP's driving manufacturing operations, things have become more demanding from the point of view of data collection. Data entry through the keyboard means loss of critical time and high chances of error.PC's have their inherited problems like, wires, space requirement, reliability etc.
This is where barcode, wireless & RFID technologies come to the rescue of the worker for data collection needs.
|
Warehousing Management |
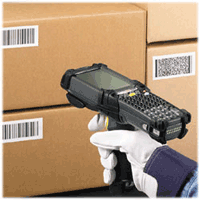 |
In manufacturing operations, the things are changing very rapidly. The manufacturing operations, which were supported by in-house systems, are now being supported by ERP systems. The companies now partner with material suppliers, logistics providers and customers in order to share costs and stay competitive. The bar code and wireless data collection is an integral part of present day manufacturing operations. With integration of bar code data collection system into manufacturing operations, the user gets the ability to enter and access real-time, accurate data right from the manufacturing or warehouse floor.
The availability of accurate and real-time data, allows you to make decisions that can reduce the warehousing of raw materials, the accumulation of buffer stock, and the inventory of finished goods. Real-time data allows the entire production process to be synchronized. With the integration of bar code, RFID and wireless technologies, you can forget about running wires. You don't have to wait around for employees to laboriously and inaccurately enter data by hand. Avoiding such human interaction, transactions move quickly and accurately from your plant floor or warehouse right into your ERP system. |
Automating Manufacturing Operations
Raw Materials Receiving:
The integration of bar coding starts right from the raw material receipts. Whether incoming material is bar coded or not, it's the place you verify items, quantities and ship dates and make certain that they conform to the terms established with your vendors. Receiving must also notify production, purchasing, incoming inspection, and accounts payable of the receipts. The bar code integration and data capture streamlines all the steps above. Instead of manually matching shipping documents against purchase orders, now this is done through bar code readers and hand held terminals. With the power of PDF417 bar codes, the supplier can print your entire shipment information as a single PDF417 bar code. As the shipment reaches the receiving gates, this PDF417 bar code is scanned either using Handheld Scanners or using Wireless Terminals. The information is instantly verified with the purchase order and material receipt is recorded in the system.
Incoming Inspection: After the receipt of the material, it should be inspected before it can be inducted into the raw material store. A formal inspection procedure should exist for each item, and should include the parameters for accepting and rejecting production material. Most of the time, the results of these inspections are recorded on paper sheets, which are subsequently keyed into system at a later date. Instead of recording all this manually, the same could be done through bar code terminals. All the inspecting person needs to do is scan the item code and then scan the result codes from a pre-defined result code list. The identity of the inspector can also be captured by scanning a bar coded identification badge as part of the inspection process. |
Inventory Management |
|
Incorporation of Bar coding can lead to a much efficient Inventory Control system in the manufacturing industry which can help reap benefits like :
- Fast and accurate information dissemination of the shipment leading to a better inventory control
- First-manufacture-first-out (FMFO) to minimize product obsolescence, minimize the inventory holding cost and maximize the freshness of the stock in case of FMCG
- Improved control over stock, warehousing and distribution of products
- Better control over reorder levels hence shorter reorder cycles
- Effective practice of just-in-time inventory control principle
- Flawless and speedy performance of periodical cycle counts
- Automated invoice generation
- Accurate and timely forecasting of raw material ordering levels
- Overall cost saving in inventory control
|
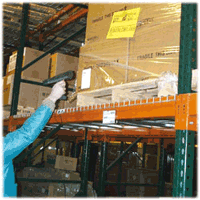 |
The cross sections of the manufacturing industry which can be benefited from bar coding are: |
- Automobile and automobile ancillaries
- Engineering products manufacturing companies
- White Goods manufacturing companies
- FMCG companies
- Textile manufacturing companies
- Pharmaceutical companies
- Any other manufacturing company with large number of raw material or products
The bar coding products required as the part of the solution are:
- Mobile Computers (MC) : You can carry out following transactions using MC's:
- Cycle Count : The stock balance as per the database can be downloaded into the Hand Held Terminal. The warehouse operator can scan the bar coded product ID and obtain the actual balance of the product there at warehouse against the downloaded balance thus performing an efficient cycle count.
-
Receipts : The goods receipt information like the product ID, quantity being shipped etc. can be downloaded into the terminal. Actual receipt can be verified against the pre-received information by scanning the bar coded information and obtaining the actual quantity shipped.
-
Dispatches : The pickup list/loading slip having the information like the product ID, quantity to be shipped, bay/bin no. can be downloaded into the terminal and the actual shipment can be verified and controlled by matching the same against the downloaded information.
- Thermal Transfer Printer : On receipt of the goods at the warehouse the bar code labels can be printed to bar code the products coming from various factories if not already bar coded at the factory end. Different categories of printers like light duty, medium duty and heavy duty printers are available to cater to various intensities of printing needs.
- Bar Code Generation Software : Bar code generation software is needed for designing and printing labels. Bar codes complying with various 1D and 2D symbologies can be generated, which can be printed on a large variety of the printers. Data source ranges from keyboard entry to the various databases through the ODBC support. It can also be attached to other host applications through the ActiveX support.
|
Shopping & Distribution |
|
Once the material is received in the raw material stores, it has to be issued to the shop floor. Keeping track of the material consumed in WIP could be a difficult task. However, with the help of bar coding, the same can be achieved very easily. The bar code of the raw material being issued to production is scanned against the bar codes production/work order.
When all the operations, work centers and control points are bar coded, by just simply scanning the bar coded production label, you can achieve real-time material consumption and WIP status very easily.
We provide complete range of barcode equipments like Fixed Mount scanners to track your products moving on the conveyers, Hand Held Terminals (Batch or Wireless) to feed in your data related to production operations directly from the shop floor, thus enabling you to track and compute Work-in-Process at any point of time. |
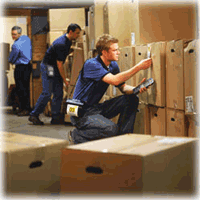 |
Apart from this, we can also help you in collecting data from other shop-floor equipments (e.g. PLC's, Weighbridges, or other devices capable of giving data on Serial/RS232 port) using our middleware integration technologies. |
Work-in-Process (WIP) Tracking |
|
Once the material is received in the raw material stores, it has to be issued to the shop floor. Keeping track of the material consumed in WIP could be a difficult task. However, with the help of bar coding, the same can be achieved very easily. The bar code of the raw material being issued to production is scanned against the bar codes production/work order.
When all the operations, work centers and control points are bar coded, by just simply scanning the bar coded production label, you can achieve real-time material consumption and WIP status very easily.
We provide complete range of barcode equipments like Fixed Mount scanners to track your products moving on the conveyers, Hand Held Terminals (Batch or Wireless) to feed in your data related to production operations directly from the shop floor, thus enabling you to track and compute Work-in-Process at any point of time.
|
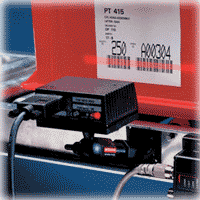 |
Apart from this, we can also help you in collecting data from other shop-floor equipments (e.g. PLC's, Weighbridges, or other devices capable of giving data on Serial/RS232 port) using our middleware integration technologies. |
|